Alors que l’impression 3D traditionnelle peine à concilier vitesse, coût et qualité, une équipe de chercheurs de l’Institut Beckman explore une voie inédite inspirée des mécanismes naturels. Leur méthode, baptisée « impression par croissance », imite l’expansion progressive des troncs d’arbres pour produire des pièces polymères à une vitesse surprenante, sans moules ni équipements coûteux. Une réinvention des processus manufacturiers qui pourrait redéfinir les limites de la production industrielle
L’impression par croissance s’appuie sur une réaction chimique auto-entretenue pour solidifier un polymère liquide en quelques secondes. Le procédé, décrit dans Advanced Materials, utilise une résine appelée dicyclopentadiène (DCPD), chauffée localement pour déclencher une polymérisation en chaîne. Cette réaction, nommée FROMP (frontal ring-opening metathesis polymerization), se propage à 1 mm par seconde — soit 100 fois plus vite qu’une imprimante 3D domestique.
« La plupart des technologies manufacturières reposent sur des moules en métal ou des fours de polymérisation, coûteux et encombrants pour les grandes pièces », explique Sameh Tawfick, professeur en génie mécanique et coordinateur du projet. « Notre approche élimine ces contraintes en exploitant la chaleur résiduelle de la réaction elle-même. »
Un procédé aussi simple qu’ingénieux
La méthode consiste à immerger un récipient de verre rempli de résine dans de l’eau glacée. Un point central est chauffé à 70°C, déclenchant une solidification en forme de sphère qui se développe comme une vague thermique. Les chercheurs contrôlent la forme finale en manipulant cette sphère durcie : en la soulevant, en la tournant ou en l’immergeant à nouveau. Pour créer une bordure ondulée, par exemple, ils soulèvent légèrement la pièce, marquent une pause, puis répètent le geste.
« C’est comparable au travail du verre soufflé, où l’artisan modifie la forme en jouant avec la température et les mouvements », compare Philippe Geubelle, coauteur et spécialiste en génie aérospatial. « Nous avons même développé un outil de modélisation prédictive pour anticiper ces déplacements. »
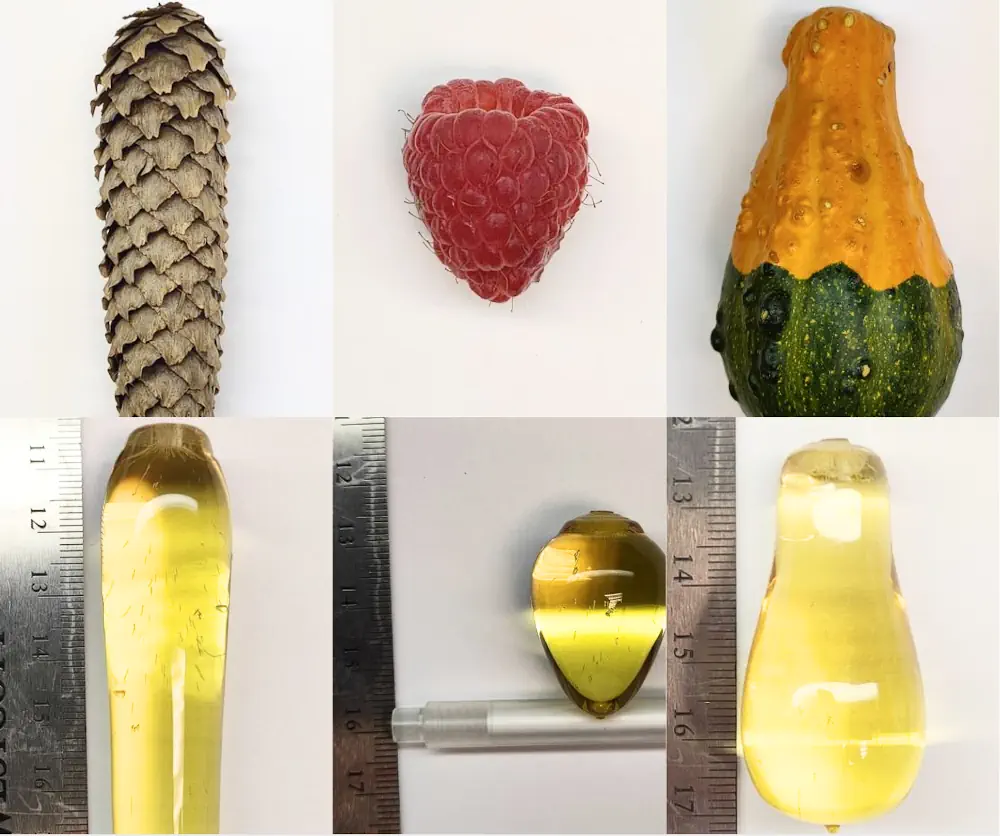
Limites naturelles et perspectives industrielles
Si l’impression par croissance excelle avec les formes symétriques — comme une courge ou un oiseau kiwi miniature —, les structures complexes restent un défi. « Fabriquer un cube parfait est impossible, tout simplement parce que la nature n’en produit pas », souligne Tawfick. « Notre procédé reflète cette logique organique. »
Malgré ces contraintes, l’équipe envisage des applications ambitieuses, notamment pour les pales d’éoliennes ou les coques de bateaux. Financé par le département américain de l’Énergie, le projet incarne selon Tawfick « une science fondamentale porteuse de ruptures industrielles ».
L’outil de simulation développé par l’équipe prévoit avec précision les mouvements nécessaires pour obtenir une forme cible. « Ce mariage entre chimie, mécanique et algorithmes illustre la force des collaborations interdisciplinaires », affirme Yun Seong Kim, doctorant et premier auteur de l’étude.
Randy Ewoldt, coauteur et professeur en génie mécanique, ajoute : « Les avancées ici décrites découlent d’un travail d’équipe exceptionnel. La culture de l’excellence collaborative de l’Illinois a été déterminante. »
Légende illustration : Les chercheurs ont utilisé leur méthode pour créer un petit oiseau kiwi.
Article : « Morphogenic growth 3D printing ». DOI : 10.1002/adma.202406265