Une équipe de chercheurs américains a utilisé une nouvelle méthode d’impression 3D pour produire une construction métallique complexe qui n’était auparavant possible qu’avec la soudure : la fusion de deux métaux en une seule structure.
À l’aide d’un processus avancé de fabrication additive connu sous le nom de fusion laser multimatériaux sur lit de poudre – rendu possible par un système nouvellement acquis par le Centre pour le traitement innovant des matériaux par dépôt numérique direct (CIMP-3D) de Penn State – les chercheurs ont imprimé une structure complexe à partir d’un mélange d’acier inoxydable à faible teneur en carbone et de bronze, qui se compose de 90 % de cuivre et de 10 % d’étain. Les chercheurs ont publié leur approche dans la revue npj Advanced Manufacturing.
« Dans un processus appelé dépôt sélectif de poudre, nous pouvons désormais faire fondre plusieurs métaux en poudre en une seule couche pendant le processus de fabrication additive – et nous avons été la première université américaine à le faire », a dit Jacklyn Griffis, candidate au doctorat en génie mécanique et première auteure de l’article. « Les poudres fines ont un diamètre de quelques dizaines de microns, presque comme de la farine. Nous pouvons déposer sélectivement la poudre avec une résolution de l’ordre du micron, puis la faire fondre à l’aide d’un laser ».
Les chercheurs ont utilisé un système de dépôt sélectif de poudre Aerosint, que CIMP-3D a acquis en août 2023, pour imprimer et tester la pièce métallique. Le système a été intégré à une machine 3D Systems ProX320 AM existante dans le laboratoire SHAPE (Systems for Hybrid-Additive Process Engineering) du CIMP-3D. Une pièce métallique d’un centimètre de haut comprend des milliers de couches de poudre métallique, explique M. Griffis, et il faut quelques heures pour l’imprimer.
« Nous disposons désormais de la technologie de traitement nécessaire pour imprimer ces pièces métalliques multi-matériaux, ainsi que d’un moyen de surveiller le bain de fusion, d’observer et de résoudre les problèmes potentiels en temps réel », a ajouté l’auteur correspondant, Guha Manogharan, professeur agrégé de génie mécanique, directeur du laboratoire SHAPE et codirecteur du CIMP-3D. « Pour ce faire, nous produisons un rendu numérique en 3D de la pièce par tomodensitométrie, que nous utilisons pour rechercher des pores, des fissures à l’interface ou des défauts à l’échelle du micron. »
En imprimant simultanément deux métaux dans une seule poudre, les chercheurs ont dû répondre à des questions complexes sur les conditions de traitement et la qualité des pièces. Dans cet article, ils se sont concentrés sur l’analyse de l’orientation de la pièce pour comprendre ce qui changerait si la pièce était imprimée à l’endroit, à l’envers ou sur le côté.
« Dans notre analyse, nous avons relié l’orientation de la pièce à un certain nombre d’observations sur la structure, notamment les défauts tels que les fissures et la porosité, les microstructures interfaciales et la manière dont les éléments sont diffusés ou mélangés à travers l’interface », explique M. Griffis. « Nous avons ensuite établi un lien entre ces défauts imprimés et les performances de la pièce.
Leur structure finie est une forme complexe connue sous le nom de gyroïde, qui est utilisée dans des applications telles que les échangeurs de chaleur et les implants biomédicaux. Les chercheurs ont choisi la forme gyroïde pour démontrer les capacités du nouveau processus de fabrication – seule la fusion laser sur lit de poudre multi-matériaux peut créer une forme gyroïde multi-matériaux.
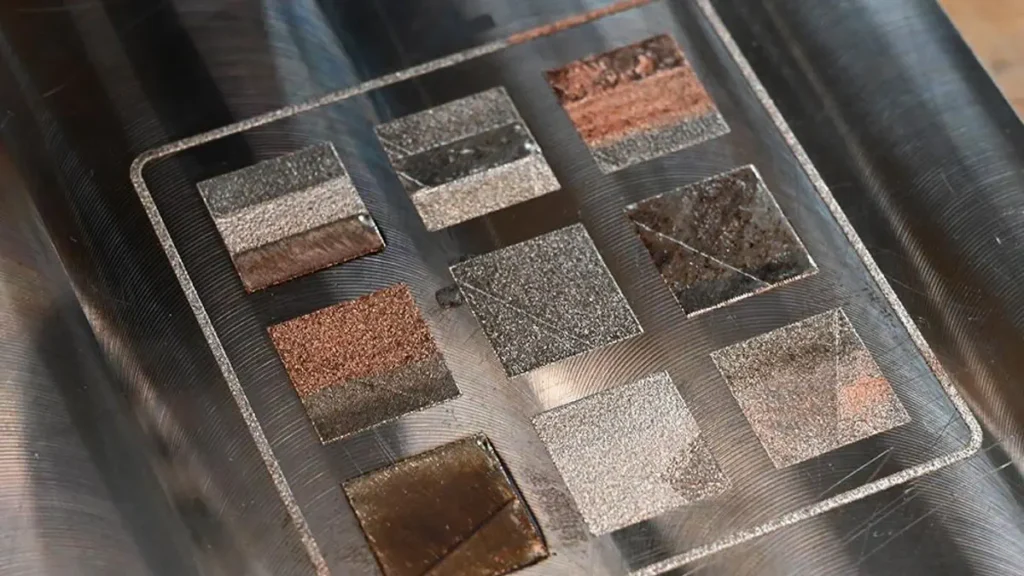
« Penn State a toujours été un leader dans le domaine de la fabrication additive métallique, mais nous avons désormais la capacité de fabriquer des pièces multimatériaux complexes, ce qui nous permet non seulement de réaliser des conceptions complexes, mais aussi de contrôler avec précision l’emplacement de chaque matériau », a commenté M. Manogharan. « Pour parvenir à une production complète, nous devons comprendre les causes des défauts en fonction des matériaux et des conditions de fabrication afin de répondre à la question de savoir pourquoi les pièces ont échoué au niveau des interfaces.
Dans de futures études, les chercheurs utiliseront un système de contrôle en cours de fabrication pour transformer la méthode d’impression 3D en une méthode plus robuste et prête pour la production. Ils prévoient également d’incorporer d’autres alliages métalliques dans la fusion multi-matériaux sur lit de poudre laser, tels que l’Inconel et le cuivre.
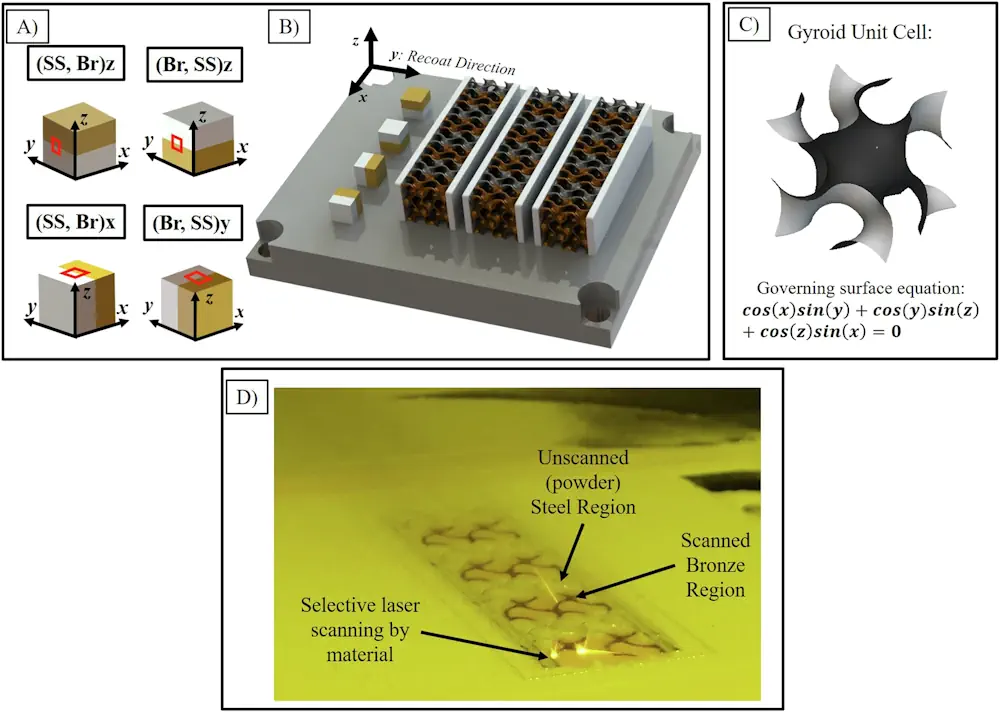
Légende illustration : Rendu volumique par micro-TDM de la poutre gyroïde multi-matériaux, fabriquée à partir d’acier inoxydable à faible teneur en carbone (en bleu) et de bronze (en orange), à l’aide du système de dépôt sélectif de poudres Aerosint. Crédit : fourni par le laboratoire SHAPE, CIMP-3D et le Centre d’imagerie quantitative de l’État de Pennsylvanie.
Outre Griffis et Manogharan, les coauteurs sont Kazi Shahed, étudiant diplômé de Penn State en ingénierie industrielle et de fabrication ; Matthew Lear, professeur de recherche associé en sciences de l’ingénierie et en mécanique et affilié au laboratoire de recherche appliquée ; Kenneth Meinert, professeur de recherche adjoint à la retraite et affilié au laboratoire de recherche appliquée ; et Buket Yilmaz, ancien élève du programme d’études supérieures en ingénierie mécanique de Penn State.
Article : « Multi-material laser powder bed fusion: effects of build orientation on defects, material structure and mechanical properties » – DOI : s44334-025-00020-5