Une nouvelle méthode permet d’utiliser les déchets de laine de roche et de béton comme nouveaux matériaux de construction dans le cadre d’un processus qui élimine également le CO2 d’un flux gazeux ponctuel. Il en résulte un béton dont l’empreinte carbone est réduite, ce qui permet de résoudre deux problèmes en même temps.
Des réacteurs de différentes tailles répartis dans cinq laboratoires du campus DTU de Lyngby pourraient bien détenir le secret permettant d’éviter l’envoi à la décharge de matériaux de construction non recyclables, en les transformant en nouveaux matériaux de construction. Cette méthode est le fruit de l’imagination de Susan Stipp, professeur au DTU.
En bref, elle utilise de la laine de roche* usagée et du béton usagé concassé dans de l’eau, dans des conteneurs, où l’on ajoute du CO2 et un mélange breveté de molécules naturelles spécialement développées.
Les déchets de matériaux de construction, qui sont alcalins, sont transformés en un produit à grains fins contenant du carbonate de calcium et d’autres minéraux.
Ce produit s’accumule sous forme de sédiments dans les conteneurs, à l’instar du tartre qui s’accumule au fond d’une bouilloire lorsque l’on fait bouillir de l’eau. Ce matériau solide possède des propriétés qui le rendent approprié comme ingrédient du béton. Il peut remplacer partiellement le ciment, dont l’empreinte carbone est importante.
« Le béton fabriqué à partir de ce produit ne sera probablement pas assez solide pour construire de grands bâtiments, mais il pourrait être utilisé pour fabriquer des pavés dont l’empreinte carbone serait plus faible », indique Susan Stipp.
Se concentrer sur la montée en gamme
Grâce à une bourse Grand Solutions du Fonds danois pour l’innovation, Susan Stipp et ses collègues ont travaillé sur cette idée pendant des mois dans le cadre du projet CO2Fix et ont démontré la « preuve du concept ». Lors d’essais menés dans de petits conteneurs (appelés réacteurs), ils ont montré que le CO2** est immobilisé en tant que composant du nouveau matériau.
Le travail en laboratoire se concentre désormais sur l’ajustement du processus et des additifs afin que la production puisse être augmentée avec les mêmes bons résultats. Les chercheurs sont passés de minuscules réacteurs de 50 ml à des réacteurs de 1 et 20 litres, puis à un réacteur de 4 mètres de haut pouvant contenir 300 litres.
« C’est comme pour un gâteau. On peut doubler la recette et obtenir un bon gâteau, mais on ne peut pas la multiplier par 10 ou 100 et être sûr qu’elle fonctionne. Vous devrez peut-être ajuster les ingrédients ou la façon dont vous mélangez les choses, ou encore le faire cuire à une température différente », explique le professeur.
Une fois que les chercheurs auront maîtrisé le processus dans le grand réacteur du laboratoire, ils ont l’intention de construire une installation pilote au sein de l’entreprise de valorisation énergétique des déchets ARGO à Roskilde, qui est l’un des partenaires du projet. Le CO2 capturé dans les gaz de combustion de l’incinération des déchets sera introduit dans le réacteur CO2Fix, où il sera « minéralisé », c’est-à-dire converti en matériaux utilisables dans la fabrication de nouveaux bétons.
Le potentiel du projet enthousiasme le directeur adjoint d’ARGO, Klaus W. Hansen, qui travaille à l’amélioration du climat et à l’économie circulaire : « Si nous réussissons ce projet, nous aiderons le climat en réduisant les émissions de CO2 tout en retirant un matériau de la décharge et en le transformant en un nouveau matériau de construction de valeur. »
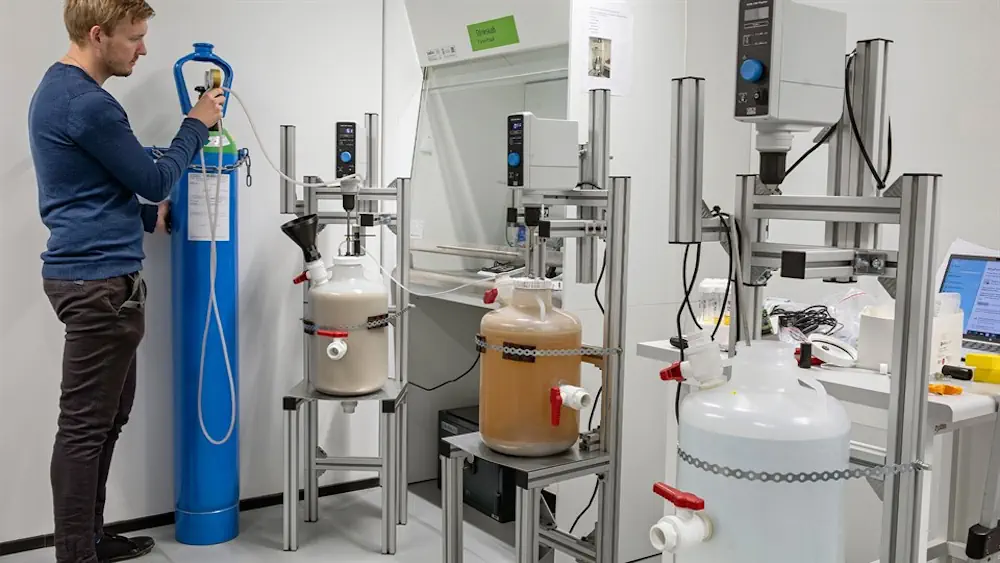
Des avantages multiples
Il n’y a pas que l’environnement qui bénéficie de la réduction des déchets de construction dans les décharges, ou le climat qui bénéficie du CO2 capturé et stocké dans les nouveaux produits en béton.
« Nous savons que certaines parties du matériau que nous produisons peuvent être utilisées comme charge dans le ciment, et nous travaillons intensément pour qu’il puisse remplacer une partie du ciment, car cela augmentera la valeur du produit que nous fabriquons. L’élimination du CO2 des gaz de combustion permet également de réaliser des économies considérables, car elle évite de devoir payer la taxe carbone sur les émissions », souligne Susan Stipp.
L’objectif est d’installer des réacteurs dans les entreprises danoises qui doivent éliminer le CO2 de leurs gaz de combustion. La fabrication d’un solide à partir du CO2 rendra le Danemark moins dépendant de l’expédition du CO2 capturé vers la Norvège, où il sera stocké sous terre, explique Susan Stipp, et contribuera à créer des emplois danois pour la production et l’entretien des réacteurs et la création des molécules nécessaires pour accélérer le processus.
* La laine de roche – populaire en tant qu’isolant et support de culture Beaucoup de gens connaissent la laine de roche en tant que matériau isolant qui garde nos bâtiments agréablement chauds en hiver et frais en été. Mais la laine de roche est aussi un support de croissance très apprécié pour les tomates et autres plantes en serre. Elle permet aux jardiniers de contrôler avec précision les applications d’engrais et de pesticides. La laine de roche est composée à 98 % d’air, mais même lorsqu’elle est broyée avant d’être mise en décharge, les déchets de laine de roche occupent encore beaucoup d’espace.
** Les émissions de CO2 liées à la production de ciment Le béton utilisé par l’industrie de la construction est produit à partir de ciment, qui contient une grande quantité de craie ou de calcaire brûlé. La combustion du calcaire nécessite de la chaleur et le calcaire lui-même émet du CO2. La production de ciment représente actuellement environ 8 % des émissions mondiales de CO2, selon les chiffres du Forum économique mondial. Outre DTU et ARGO, les autres partenaires du projet CO2Fix comprennent ROCKWOOL, qui fabrique de la laine de roche, et IBF, le plus grand producteur de béton du Danemark.
Légende illustration : Le coordinateur technique Petros Kanelis prépare la laine de roche mise au rebut qui sera placée dans des réacteurs où elle sera transformée en un produit pouvant être utilisé à la place d’une partie du ciment nécessaire à la fabrication du béton. Photo : Sine Fiig