Alors que la consommation énergétique des robots industriels alimente débats et défis environnementaux, une équipe de chercheurs allemands propose une alternative audacieuse. Leur approche, fondée sur des matériaux intelligents, pourrait redéfinir les standards de l’automatisation tout en divisant par dix la dépense énergétique. Une innovation qui s’apprête à sortir des laboratoires pour investir les ateliers.
Les systèmes de préhension traditionnels, souvent pneumatiques, cumulent les inconvénients : bruit, usure mécanique, rigidité des mouvements et dépendance à un apport continu d’énergie. Les chercheurs de l’université de Sarre ont contourné ces limites en exploitant les alliages à mémoire de forme (AMF), des matériaux capables de retrouver leur configuration initiale après déformation. Composés de nickel-titane, ces fils ultrafins agissent à la fois comme actionneurs et capteurs, éliminant le besoin de composants externes.
« Nous contrôlons ces systèmes en temps réel via une simple impulsion électrique », indique Paul Motzki, directeur scientifique du projet. Les fils AMF se contractent sous l’effet Joule, exerçant des forces équivalentes à 10 kg par fil de 0,5 mm de diamètre. Une fois l’énergie coupée, ils retrouvent leur longueur originale sans assistance. Cette propriété permet aux préhenseurs de maintenir des pièces en place sans consommer d’électricité, même lors de manipulations inclinées ou prolongées.
Des prototypes polyvalents et adaptables
Deux modèles phares seront présentés au salon Hannover Messe 2025. Le premier, un préhenseur à mâchoires, combine vitesse et précision pour saisir des objets avec une force de quatre newtons. Son architecture modulaire permet d’adapter la course des mâchoires et l’intensité de la pince selon les besoins. Le second prototype, un préhenseur à vide, utilise des doigts flexibles équipés de ventouses. Un disque métallique actionné par des muscles artificiels crée un vide fonctionnel dès que les embouts entrent en contact avec une surface.
« La surveillance intégrée vérifie en permanence la qualité du vide généré », souligne l’équipe. Ces systèmes s’auto-ajustent grâce à des réseaux neuronaux entraînés à interpréter les variations de résistance électrique des fils AMF. Une particularité qui simplifie la reprogrammation à la volée, contrairement aux robots classiques souvent figés dans des séquences prédéfinies.
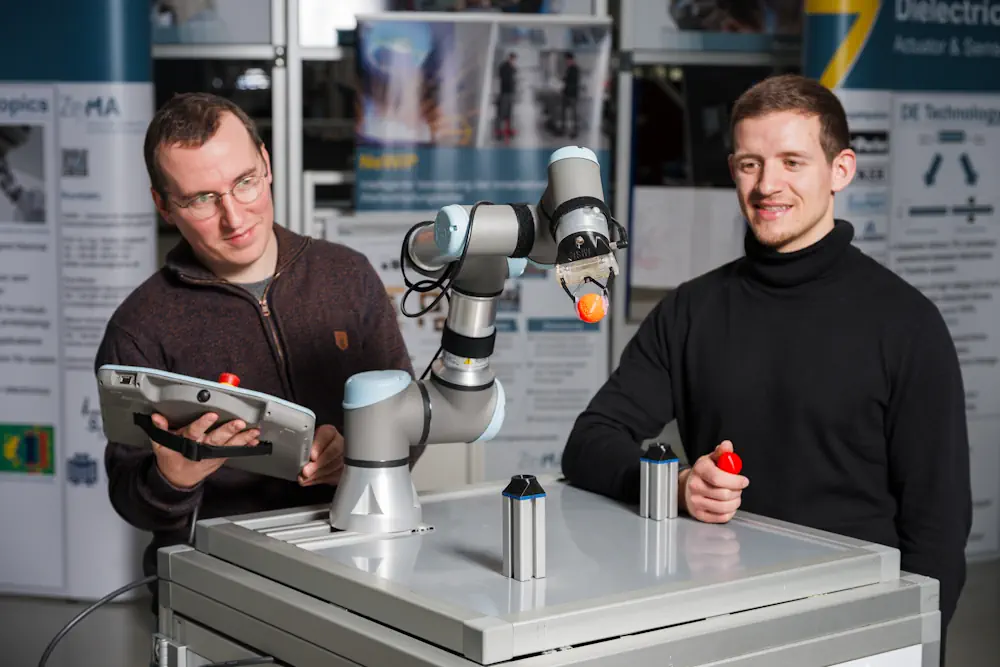
Vers une industrialisation concertée
Bien que les prototypes soient fonctionnels, leur déploiement à grande échelle nécessite des partenariats stratégiques. L’équipe sarroise cherche actuellement des industriels pour adapter cette technologie à des cas d’usage spécifiques, notamment en milieu cleanroom ou pour la manipulation d’objets fragiles. Les applications pourraient s’étendre aux valves intelligentes ou aux systèmes de refroidissement innovants, déjà explorés dans le cadre du projet européen iSMAT.
Financés par la région Sarre et des acteurs comme Bosch, les chercheurs ont publié leurs travaux dans des revues à fort impact scientifique. Leur record mondial – 5 newtons à 200 Hz avec des fils de 0,025 mm – témoigne d’une maîtrise poussée des propriétés des AMF. « Nous modulons épaisseur et nombre de fils pour optimiser force et fréquence », explique Motzki, soulignant la flexibilité du procédé.
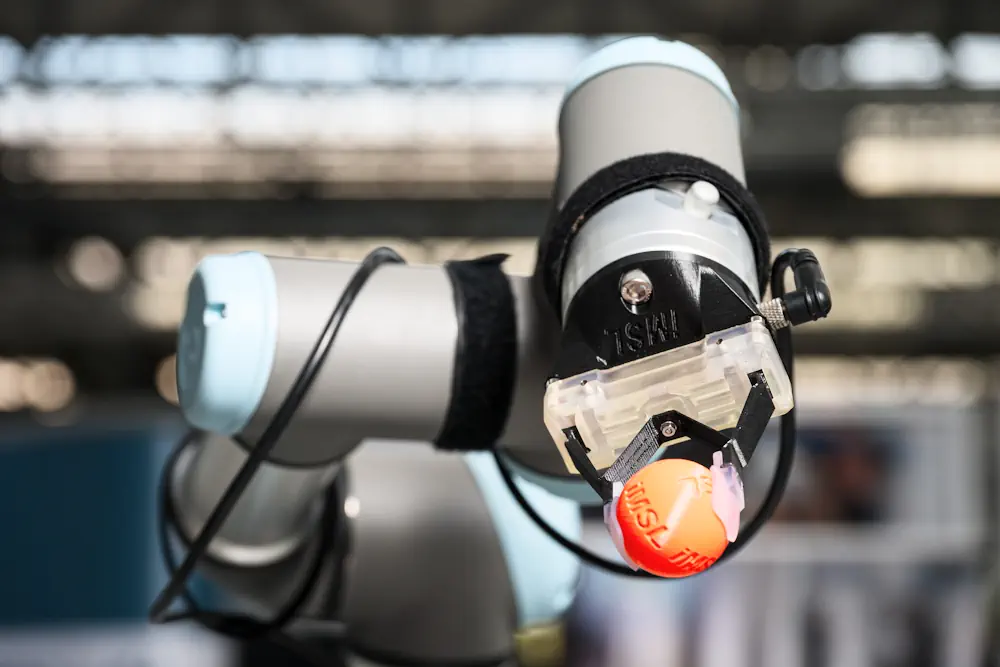
Des fondations scientifiques solides
L’innovation repose sur des années de recherche fondamentale. Les AMF exploitent un changement de structure cristalline sous l’effet de la chaleur, phénomène découvert dans les années 1960 mais longtemps resté confidentiel. L’équipe a transformé ce principe en solution industrielle viable en résolvant deux défis majeurs : la durée de vie des fils et leur réponse en temps réel. Leur intégration dans des robots compacts ouvre des perspectives pour la miniaturisation des chaînes de production.
« Les économies dépassent 90% par rapport aux systèmes pneumatiques », affirme-t-on à Sarre. Une réduction qui pourrait bouleverser l’économie des usines, tout en limitant l’empreinte carbone d’un secteur représentant 40% de la consommation électrique mondiale. Les visiteurs du stand B10 de Hannover Messe découvriront une technologie où chaque impulsion électrique compte, et où l’intelligence des matériaux remplace la complexité mécanique.
Légende illustration : Le professeur Paul Motzki (photo) et son équipe de recherche présentent à la foire de Hanovre des prototypes de systèmes de préhension robotisée, qui permettent d’alimenter et de manipuler les outils de manière énergique et sûre, notamment le Vakuumgreifer (liens, ce dernier contient une plaque de métal) et le Zangengreifer (à droite, avec une boule). Le professeur Paul Motzki (photo) et son équipe de recherche présentent des prototypes de leurs systèmes de préhension robotisés à la foire de Hanovre de cette année. Les pinces, qui peuvent maintenir et manipuler des pièces en toute sécurité et sans avoir besoin d’une alimentation continue en énergie, se présentent sous différentes formes, telles que les pinces à vide (à gauche, tenant une plaque d’acier) et les pinces à mâchoires (à droite, avec une bille). © Oliver Dietze