Des chercheurs américains ont développé une technique d’impression 3D innovante utilisant des hologrammes acoustiques. Cette méthode, plus rapide que les procédés existants, permet de créer des objets plus complexes. L’étude, publiée dans Nature Communications, décrit comment l’utilisation d’ondes sonores permet de polymériser rapidement des résines pour former des structures tridimensionnelles. Cette avancée pourrait avoir des applications dans des domaines variés, de la médecine à l’aérospatiale.
Une technologie basée sur le son
La nouvelle technique, appelée «impression directe par son holographique» (HDSP), repose sur l’utilisation d’hologrammes acoustiques. Ces hologrammes contiennent des images en coupe transversale du modèle à imprimer. Lorsque les ondes sonores interagissent avec la résine liquide, elles créent des réactions chimiques ultrarapides qui durcissent le matériau selon la forme désirée.
L’originalité de cette approche réside dans l’utilisation d’hologrammes sonores stationnaires. La plateforme d’impression, fixée à un bras robotique, se déplace selon un schéma prédéfini pour former l’objet final. Cette méthode permet d’imprimer simultanément plusieurs parties de l’objet, contrairement aux techniques traditionnelles qui procèdent point par point.
Muthukumaran Packirisamy, professeur au Département de génie mécanique, industriel et aérospatial de l’Université Concordia et responsable du projet, commente : «Nous pouvons changer les formes, combiner plusieurs mouvements et modifier les matériaux imprimés. Nous pouvons créer une structure complexe en contrôlant la vitesse d’alimentation si nous optimisons les paramètres pour obtenir les structures requises.»
Des avantages significatifs
Selon les chercheurs, l’HDSP présente plusieurs avantages par rapport aux méthodes d’impression 3D classiques :
- Une vitesse d’impression jusqu’à 20 fois supérieure
- Une consommation d’énergie réduite
- La possibilité de modifier le modèle en cours d’impression
- L’impression simultanée de plusieurs objets dans le même espace
Le professeur Packirisamy souligne : «Nous pouvons aussi changer l’image pendant que l’opération est en cours. Nous pouvons changer les formes, combiner plusieurs mouvements et modifier les matériaux imprimés.»
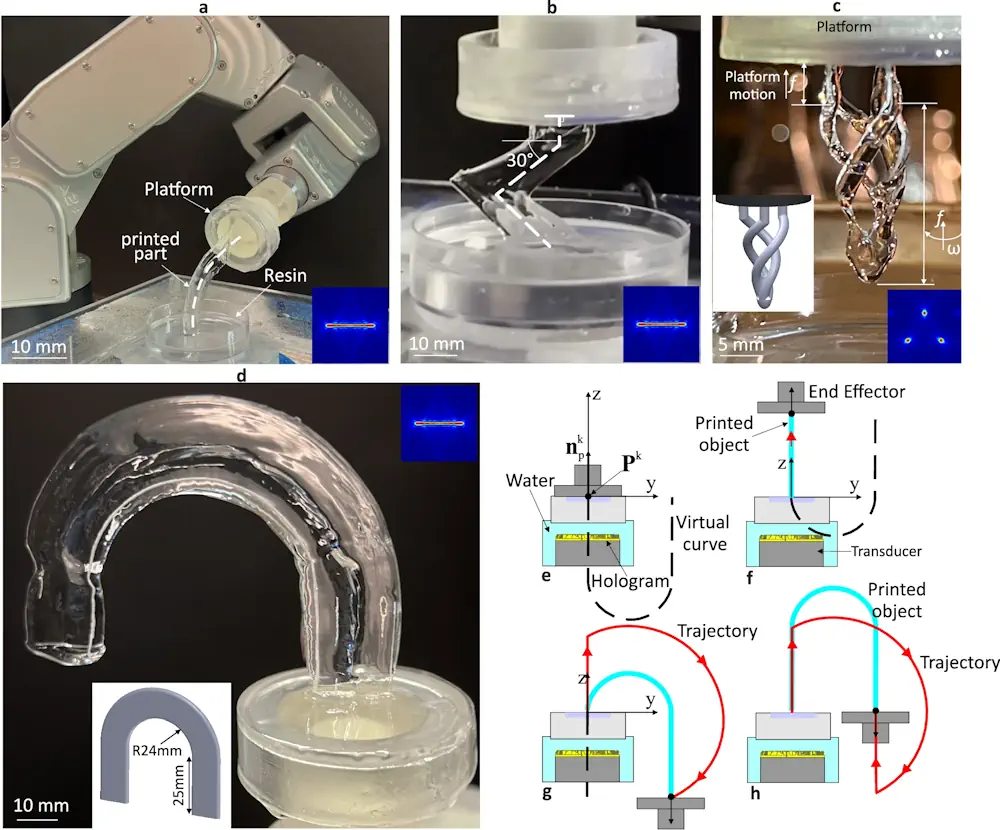
Des applications prometteuses
La polyvalence de l’HDSP ouvre la voie à de nombreuses applications dans divers domaines :
Médecine et ingénierie tissulaire
La précision de l’HDSP permet d’envisager la création de structures tissulaires complexes, de systèmes de distribution localisée de médicaments et de cellules, ainsi que des avancées en ingénierie tissulaire. Par exemple, il serait possible de concevoir de nouvelles formes de greffes de peau pour améliorer la cicatrisation ou des systèmes de délivrance de médicaments ciblés.
Impression à travers des matériaux opaques
Une caractéristique unique de l’HDSP est sa capacité à imprimer à travers des surfaces opaques. Le professeur Packirisamy précise à nouveau : «Nous pouvons imprimer derrière des objets opaques, derrière un mur, à l’intérieur d’un tube ou à l’intérieur du corps. Les techniques et les dispositifs que nous utilisons ont déjà été approuvés pour des applications médicales.»
Cette propriété pourrait permettre de réparer des organes endommagés ou des pièces délicates situées à l’intérieur d’un avion, par exemple.
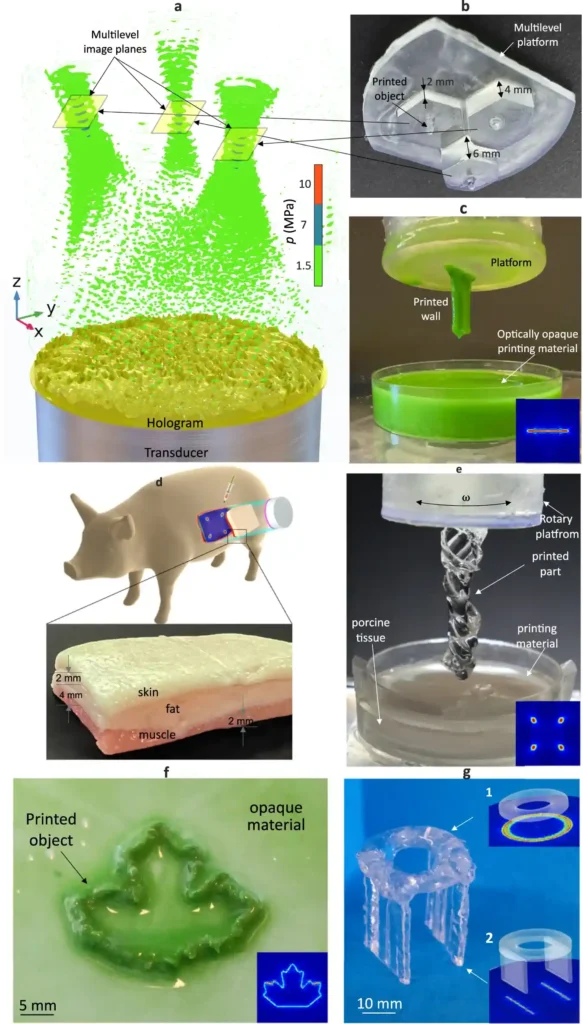
Une technologie d’avenir
Les chercheurs comparent l’impact potentiel de l’HDSP à l’évolution qu’a connue l’impression 3D basée sur la lumière. Tout comme le passage de la stéréolithographie (qui durcit la résine point par point) au traitement numérique de la lumière (qui durcit des couches entières simultanément) a marqué un progrès significatif, l’HDSP pourrait représenter un bond en avant similaire pour l’impression 3D acoustique.
L’HDSP offre également la possibilité de stocker les informations de plusieurs images dans un seul hologramme. Cela signifie que plusieurs objets peuvent être imprimés simultanément à différents endroits dans le même espace d’impression, augmentant ainsi considérablement l’efficacité du processus.
Bien que l’HDSP présente de nombreux avantages, des défis restent à relever pour son adoption à grande échelle. La maîtrise précise des hologrammes acoustiques et l’optimisation des paramètres d’impression pour différents matériaux nécessiteront des recherches supplémentaires.
Malgré ces défis, les chercheurs sont optimistes quant au potentiel de l’HDSP. Ils envisagent son utilisation dans des domaines aussi variés que la fabrication de prothèses personnalisées, la création de structures complexes pour l’industrie aérospatiale, ou encore le développement de nouveaux matériaux composites aux propriétés uniques.
Un challenge à relever pour le futur
L’impression directe par son holographique représente sans aucun doute une avancée dans le domaine de l’impression 3D. Sa rapidité, sa précision et sa capacité à imprimer à travers des matériaux opaques en font une technologie prometteuse pour des applications dans des domaines aussi variés que la médecine, l’aérospatiale et l’ingénierie des matériaux.
Alors que la recherche continue de progresser, il est probable que nous verrons émerger de nouvelles applications innovantes de l’HDSP dans les années à venir. Cette technologie pourrait bien redéfinir notre approche de la fabrication et ouvrir de nouvelles possibilités dans la création d’objets complexes et personnalisés.
Article : Mahdi Derayatifar et al, Holographic direct sound printing, Nature Communications (2024). DOI: 10.1038/s41467-024-50923-8
Légende illustration : a Schéma du processus HDSP avec la pièce imprimée sur une plate-forme montée sur un effecteur robotique, montrant le système de coordonnées de l’effecteur (ECS) et les degrés de liberté de translation (xyz) et de rotation (ωx, ωy, ωz). b Vue détaillée de la région d’impression, des bulles de cavitation sont créées près de l’image de pression cible. c Lettres « DSP » imprimées, paramètres d’impression : P = 20 W, f0 = 2,28 MHz, DC = 35%, avec leurs modèles de pression simulés correspondants, p, normalisés à la pression maximale, pmax. d Feuille d’érable imprimée, paramètres d’impression : P = 25 W, OD = 50 mm, f0 = 2,28 MHz, DC = 30%. e Paroi imprimée entièrement transparente extrudée axialement/imprimée par alimentation, f, le long de l’axe +z, paramètres d’impression : P = 6 W, OD = 25 mm, f0 = 2,24 MHz, DC = 20 %. f Hélice transparente imprimée par des mouvements de translation et de rotation de la plate-forme dans la PSHD multiaxiale. g Objet autoporté en forme de U imprimé via la trajectoire calculée du robot en utilisant les mêmes conditions d’impression qu’en (e). OD, P, f0 et DC sont respectivement la taille de l’ouverture du transducteur, la puissance acoustique, la fréquence centrale acoustique et le rapport cyclique.